Heat Treatments
50 waste thermal treatment plants are active in Italy, which process the residual part of Municipal Waste, Dry Waste, Refuse Derived Fuel and Special Waste: 35 are located in northern Italy, 7 in the centre and 8 in the south (data year 2018-2019).
Approximately 11 million tonnes of waste are sent for heat treatment, of which 6.9 million are residual urban waste, over 3.1 million are RDF, and almost 1 million are special waste from the treatment of urban waste (both hazardous and non-hazardous).
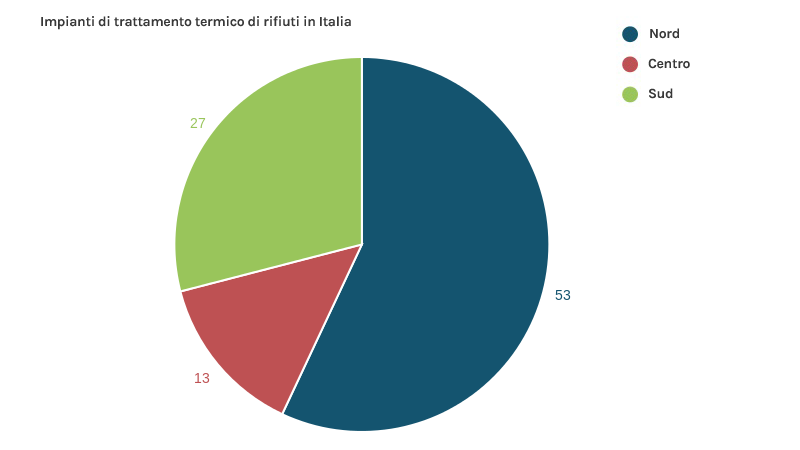
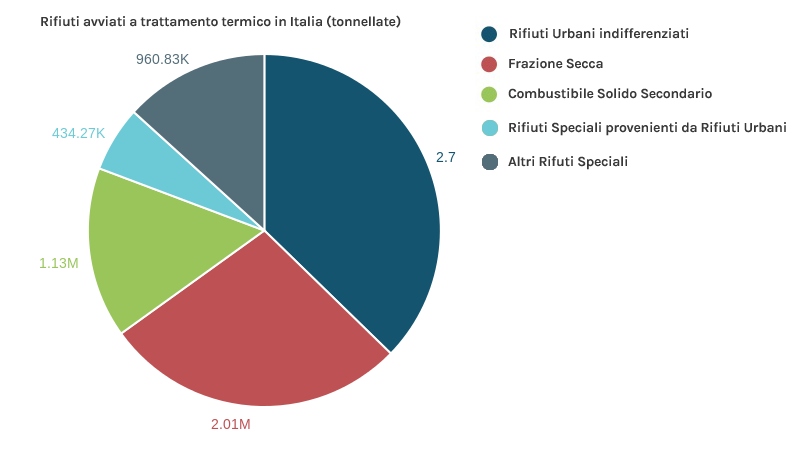
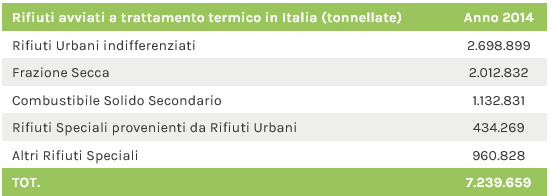
Fonte dati: Ispra 2015, 2016
Energy Recovery
Italian legislation, acknowledging European requirements for the thermal treatment of urban waste, requires that it always be associated with energy recovery (electrical and/or thermal). However, depending on the efficiency with which such recovery takes place (to be calculated on the basis of a specific formula), urban waste thermal treatment plants can be classified as energy recovery plants (defined by the legislation as “R1” treatment) or as simple disposal plants (“D10” treatment).
To date, all plants for the thermal treatment of municipal waste in Italy (37 plants, 26 in the north, 5 in the centre and 6 in the south) produce energy (electricity, heat or both combined). Energy recovery in the last 5 years has been steadily increasing. In particular, 25 plants produce electricity only, while 12 operate in cogeneration (electricity fed into the national distribution grid + heat supplied to district heating networks).
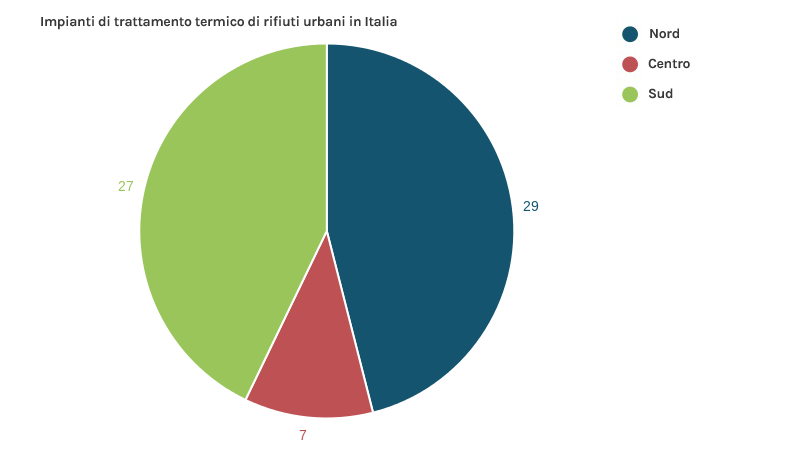
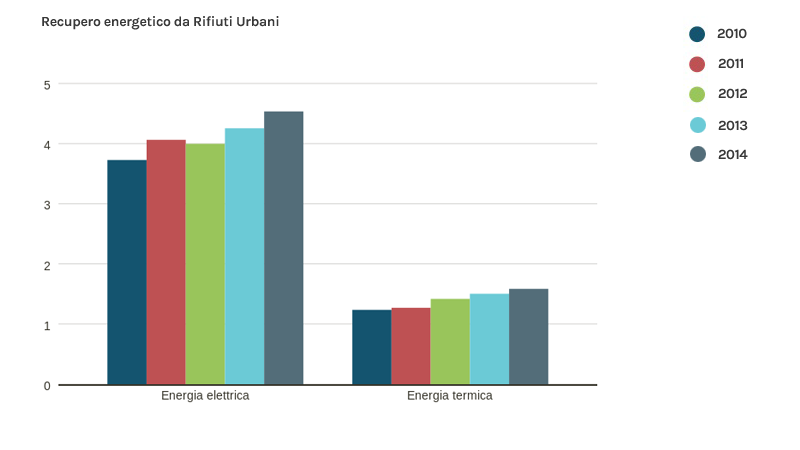
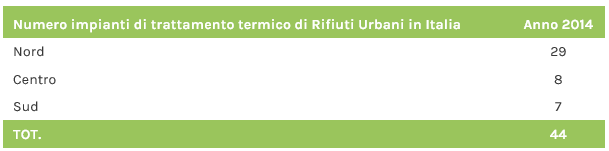

Fonte dati: Ispra 2015
Incineration
Incineration (process)
Incineration is the direct combustion of waste.
Combustion consists of the oxidation of atoms, mainly carbon (C) and hydrogen (H), to generate fully oxidized and stable compounds, mainly carbon dioxide (CO2) and water (H2O).
Combustion takes place respecting the mass balance, i.e. the mass of effluents (gaseous, such as combustion gases, and solids, such as waste) released by the process is equal to the mass of reactants (solid, such as waste, and gaseous, such as air) consumed.
Since oxidation reactions are “exothermic”, the combustion process releases significant amounts of heat.
Incineration, or thermal destruction, guarantees:
- Sanitation
- Significant reduction in volume (about 90%)
- Significant reduction in mass (about 80%).
However, it requires:
- Care in process management
- Control of gaseous emissions
- Disposal of solid residues
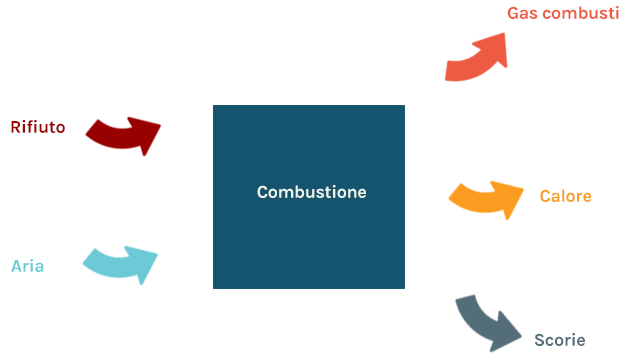
Incineration (plant layout)
A modern incinerator can be considered to all intents and purposes as a medium-small thermoelectric power station.
The incoming waste is stored in a pit where it is homogenized before being loaded into the combustor.
The most commonly used and widespread combustor technology is that with a mobile grate, horizontal or inclined, on which the waste advances, is mixed and, in contact with air, undergoes combustion, with the production of burnt gases and slags.
Other types of industrially used combustor are those with a rotating drum and fluidized bed. The former is used exclusively for industrial waste (solid and liquid) with high calorific value, while the latter is used exclusively for pre-treated waste such as RDF(Refuse Derived Fuel).
Gases produced by the combustor pass through the heat exchange section (boiler) where they release heat and cool down. The heat is used to produce steam, which in turn is used in a turbine for the production of electricity or electricity combined with heat.
Before being expelled into the atmosphere, the burnt gases undergo a series of treatments to reduce pollutants (filtration of dust, neutralization of acid gases, reduction of nitrogen oxides, absorption of micropollutants), using reagents, and production of solid and/or liquid residues. These residues are special waste that can be recovered and/or disposed of.
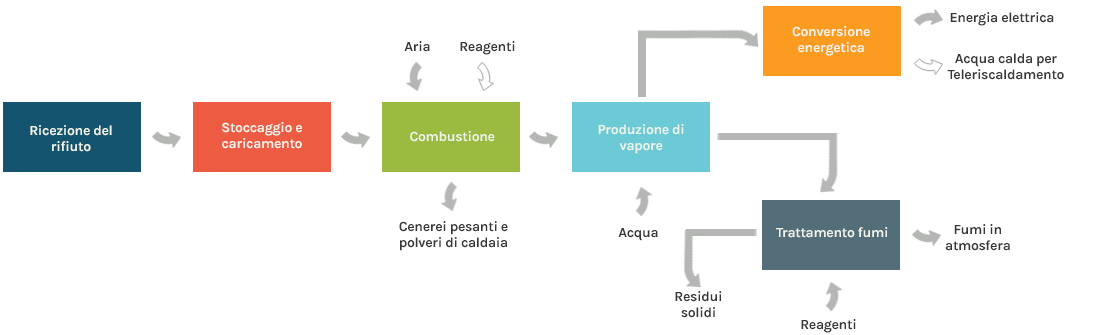
Incineration (atmospheric emissions)
Combustion gases (fumes) produced by the incineration of waste and discharged after purification into the atmosphere contain polluting species in concentrations lower than the authorized limits which are normally lower than the limits established by current legislation for industrial activities. The different types of pollutants are:
- Carbon monoxide(CO): a toxic gas, colorless and odorless, produced by incomplete combustion. Its concentration is normally limited to a few parts per million by optimizing the combustion of waste.
- Nitrogen oxides (NOx): main contributors to the formation of smog and particulate matter. Their formation is limited by optimizing the combustion of the waste, but specific removal (reduction) processes using ammonia reagents are required to meet common authorized emission limits.
- Acid gases (HCl, HF, HBr, H2SO4): create corrosion problems and are responsible for acid rain and smog. They are normally removed (neutralized) by suitable alkaline chemical reagents (lime or sodium bicarbonate).
- Particulate matter(PM): minute solids transported by fumes to which carcinogenic effects are attributed. They are normally removed by means of suitable filtration systems (electrostatic precipitators, cyclone filters, bag filters).
- Dioxins, furans (PCDD e PCDF) ) and, more generally, organic-halogen compounds: toxic compounds that are easily absorbed by living organisms. They are normally present in waste. They are thermo-destroyed by burning the waste appropriately. They can reform during the cooling of fumes, in which case they are removed (absorbed) by activated carbon.
- Metals: ssubstances that are absorbed by living organisms, which are then unable to expel them (poisoning). They concentrate in the particulate matter and are therefore removed by the filtration systems. Mercury, which is particularly volatile, is absorbed on activated carbon.
- Polycyclic Aromatic Hydrocarbons (PAHs): carcinogenic substances typically transported by particulate matter. They are controlled thanks to the efficient removal of particulate matter.
Incineration (solid residues)
Further waste combustion products comprise solid residues, which are associated both with the presence of ash in the waste (bottom and fly ash), and with the use of various reagents for the purification of fumes (light dust).
The main solid residues discharged from a waste-to-energy plant are the following:
- Bottom ash: consisting mainly of inorganic substances, such as salts and metals; may contain traces of unburnt materials (within the regulatory limit of 3% by mass on a dry basis). It is collected from the bottom of the combustion chamber, and is normally subjected to specific analyses resulting in classification as non-hazardous waste. Metals (ferrous and non-ferrous, including precious metals) can be recovered from the slag and the remaining part can be reused for the production of building materials or as a component of road foundations
- Boiler and fly ash: consisting of solid material entrained in the flue gases, it is collected in the energy recovery section of the boiler (the former) or by the dedusting system (the latter). It can be classified as either hazardous or non-hazardous waste depending on the results of specific analyses carried out periodically. It is stabilized/rendered inert and disposed of in appropriate landfills, or recovered as a filler for spent rock salt quarries.
- Residues of the flue gases treatment system (often mixed with boiler/flywheel ash): consisting of particulate not previously abated and solid compounds formed after injection of reagents. They are normally classified as hazardous waste, and can be disposed of in appropriate landfills, after being rendered inert, or recovered for the production of reagents for the treatment of regenerated fumes.
Pyrolysis
Pyrolysis is a process of thermal decomposition of organic matter present in waste that takes place in the total absence of atmospheric oxygen, at temperatures of between 300 ° C and 900 ° C: in these conditions the organic molecules are broken down and possibly recombined in simpler structures. For sustaining the process it is usually necessary to provide heat (endothermic process).
Normally, the process results in the following as its main products:
- Pyrolytic gas (syngas) mainly consisting of hydrogen (H2), methane (CH4), carbon monoxide (CO) and carbon dioxide (CO2) ;
- Solid fraction (char) ccontaining solid carbon and inorganic substances.
A gaseous mixture is extracted from the pyrolysis reactor and is condensed to separate the syngas from the condensables (oil and water): the former, after further treatments, can be used to supply heat to the pyrolysis reactor, i.e. for the production of electricity and heat; the latter undergoes a process of water separation and can be used to produce liquid fuels (through distillation) or to generate electricity and heat.
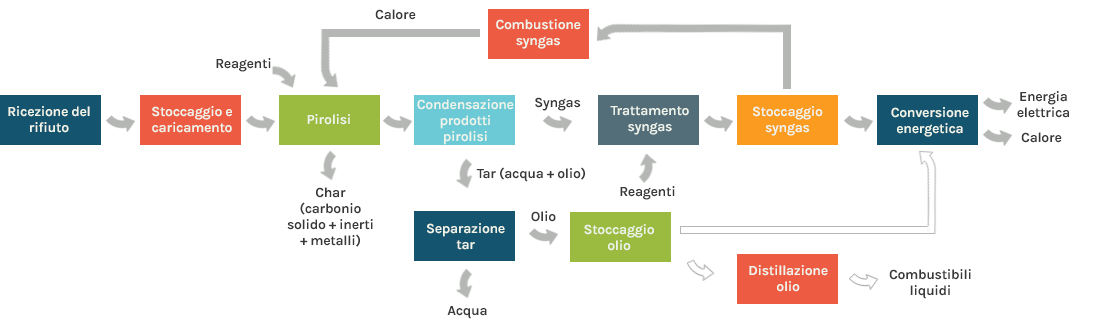
Gasification
Gasification is a partial oxidation process, carried out by carefully controlling the amount of oxygen supplied to the process: in these conditions the organic matter is both thermally decomposed and partially oxidized, in order to produce a gaseous fuel (syngas), containing fuel species such as mainly carbon monoxide (CO) e hydrogen(H2), with some methane (CH4). The gasification of the waste therefore does not aim at immediate use of its energy content, but rather its transformation into an energy vector, syngas, which can be used for the production of electricity and heat, achieving potentially higher yields than those obtainable using the waste as it is.
Syngas may contain heavy volatile compounds (tar), and can lead to the formation of solid residues (char) mainly consisting of solid carbon and inorganic substances.
Gasification can take place using different gasifying agents:
- Air: a simpler and widely used reagent, it produces a diluted syngas with low calorific value;
- Oxigen: a valuable reagent, which must be specially produced and which produces a syngas with a high calorific value;
- Steam: a reagent that produces a syngas rich in hydrogen (H2), with a high calorific value, but which requires an external heat supply.
Gasification has the following advantages:
- Greater potential for recovery of waste’s energy content compared to incineration;
- Less volume of gas to be purified compared to incineration;
- Possibility of various uses of syngas.
However, it has the following disadvantages:
- Extremely complicated process management;
- Production of difficult-to-purify syngas;;
- Presence of toxic, flammable/explosive gases at high temperatures.
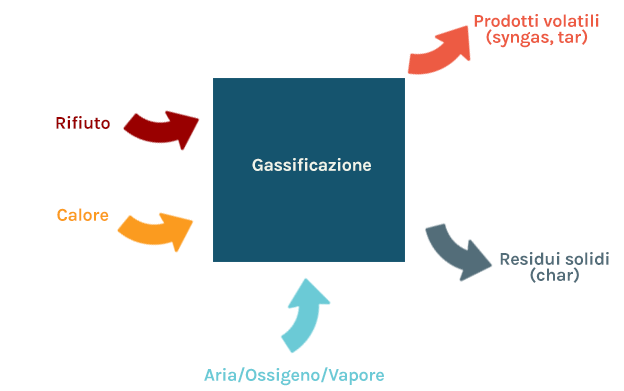